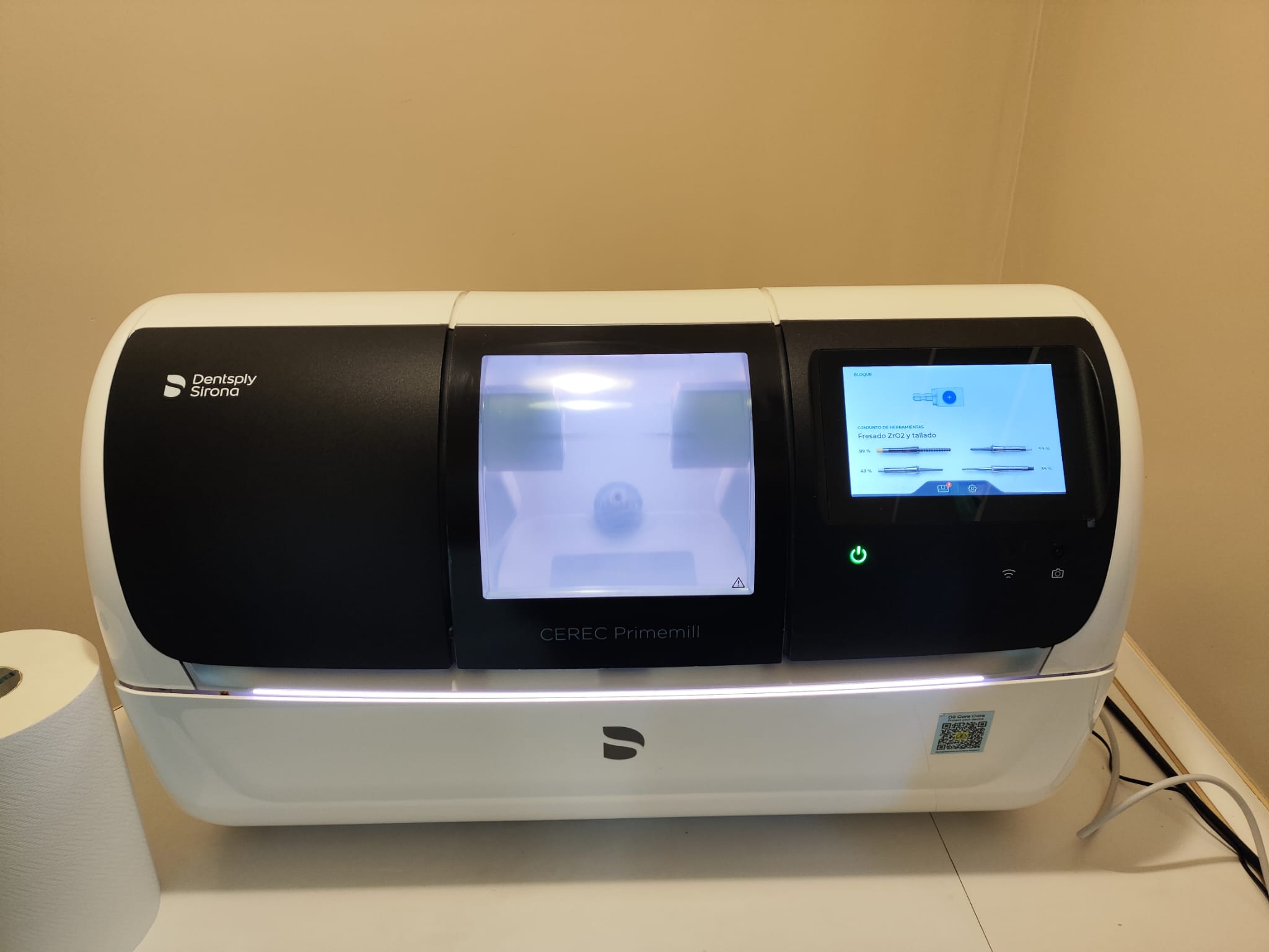
Introduction:
Milling machines are indispensable tools in modern dentistry, particularly in the realm of CAD/CAM technology. These ingenious machines carve dental restorations, implants, and appliances from a broad array of materials with pristine precision. There are three primary types of these machines: Wet Milling Machines, Dry Milling Machines, and Wet & Dry Two-in-One Milling Machines.
Wet Milling Machines:
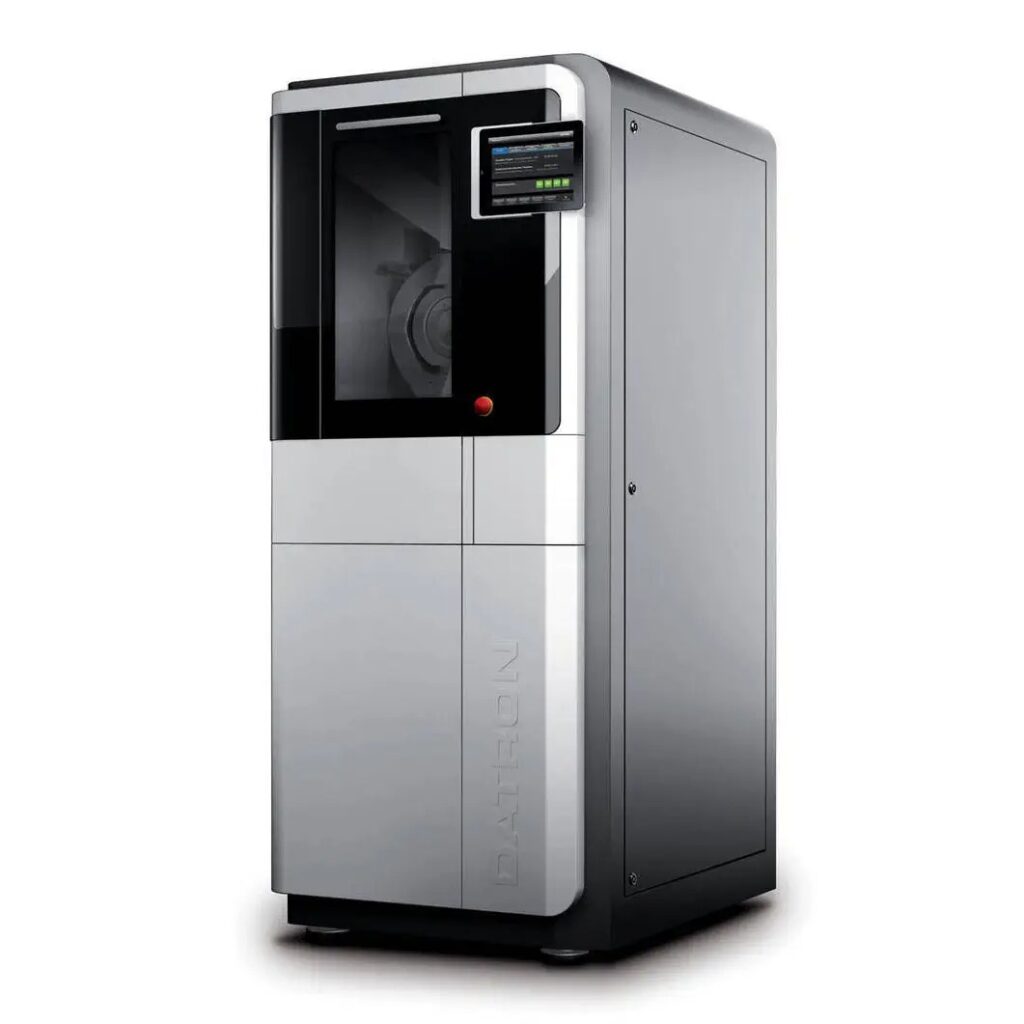
Wet millings machines utilize cutting fluid, usually water or oil-based, during the milling process. This coolant serves two central roles: to cool the milling tool, preventing overheating and thermal damage, and to flush away the material debris produced during the milling process, preserving the integrity of the final product.
Wet milling is the preferred approach when working with materials such as zirconia and lithium disilicate. These hard, brittle materials might at a higher risk of damage from the heat generated during the milling process without coolant’s compensating cooling effect. In addition, wet milling also generates a smoother surface finish on the restorations, contributing to superior aesthetics and patient comfort.
Dry Milling Machines:
Dry milling takes place without the use of cutting fluids. This machine type is the method of choice when working with certain materials, such as wax, PMMA, and specific types of resins. These materials, when subjected to wet conditions for prolonged periods, might absorb moisture, altering their physical properties and negatively impacting the restoration.
Dry milling is faster, given the absence of the requirement to dry the restoration after milling. However, the absence of coolant can lead to increased heat generation, so dry milling is better suited for materials that are not highly susceptible to thermal damage.
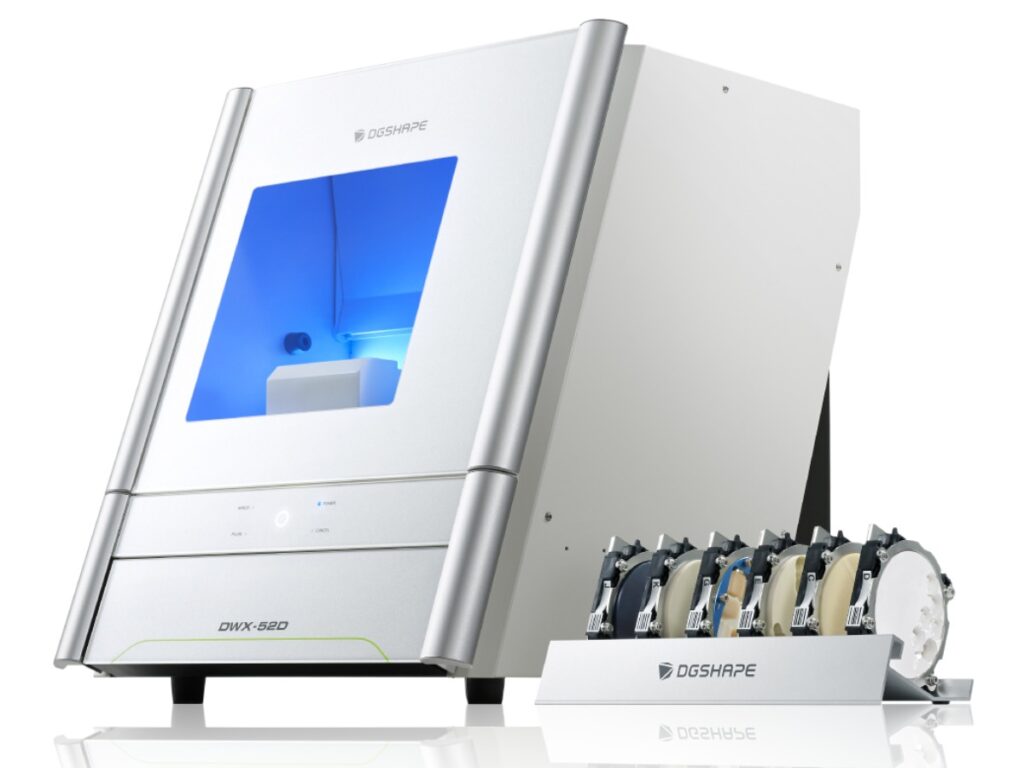
Wet & Dry Two-in-One Milling Machines:
Wet & Dry Two-in-One Milling Machines offer a fusion of the capabilities of both wet and dry milling machines. They are equipped to handle a wide spectrum of materials – from zirconia, ceramics, and metal alloys to resins and wax.
These dual machines are designed to switch seamlessly from wet to dry milling, or vice versa, based on the material used, thus eliminating the need for separate machines. This versatility safeguards that all materials are optimally processed in the conditions that best suit their physical properties.
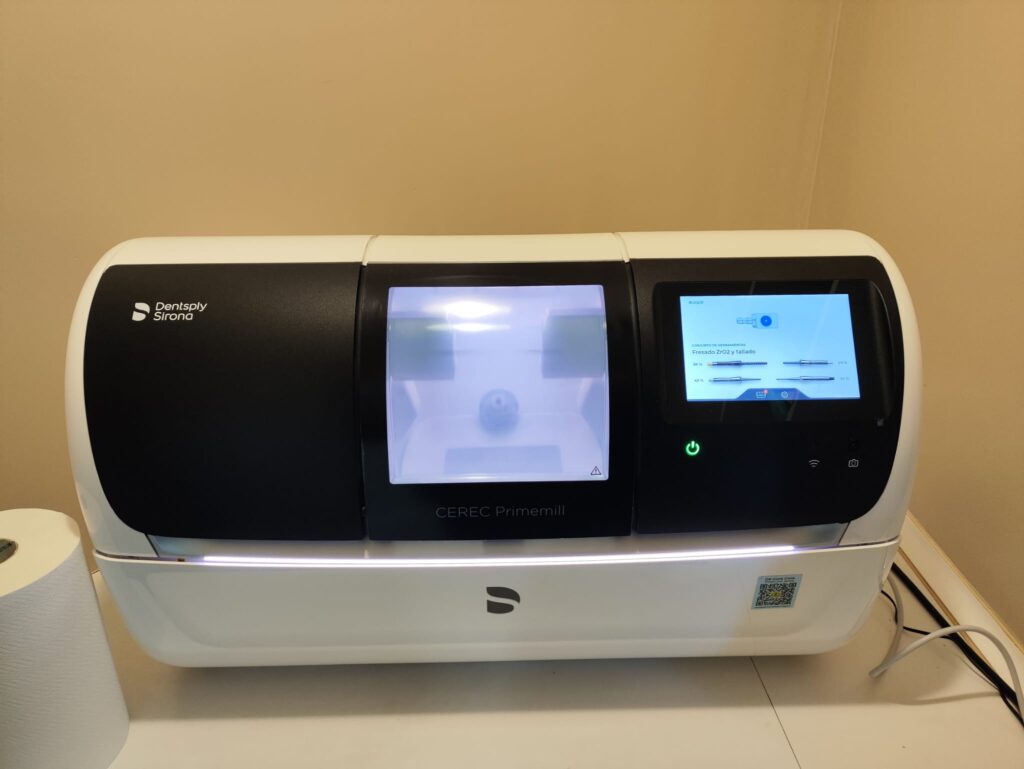
Conclusion:
Wet milling machines, dry milling machines, and wet & dry two-in-one milling machines each bring their unique benefits to the dental laboratory, expanding the lab’s capabilities and its ability to deliver bespoke dental solutions to patients. Regardless of the machine type, the detail and precision with which these devices operate are astounding, creating restorations that mimic natural teeth impeccably.
As the dental industry continues to evolve with ever-changing technology, this advanced machinery – whether wet, dry, or two-in-one – will undoubtedly continue to play a significant role, streamlining workflows, and enhancing the precision and quality of dental restorations. The ability to adapt and work with a vast and growing range of materials will be key to meeting the diverse needs of patients, whether in terms of aesthetics, function, durability, or biocompatibility. The choice between wet, dry, or two-in-one milling machines will primarily depend on the specific needs and capabilities of a particular dental lab.
Leave a Reply